The Nuclear industry often requires large radiation shields made primarily from lead. One common method is to pour lead into a steel fabrication. The metal shell protects the lead in a durable casing that holds up better over time. This also ensures that any risk of lead exposure is minimized as the lead is sealed in an outer casing. MarShield is a North American leader in nuclear lead pours and through this blog, we aim to highlight:
- Some of the steps we use in producing a high-quality pour
- Key considerations when designing a fabrication to be filled with lead for radiation shielding
Fabrication Construction and Design
To start, the fabrication needs to be designed and built to suit the shielding needs and to allow for the greatest success when filling with lead. The designing process is as follows:
- The base alloy composition: The fabrication needs to be made from a minimum of ¼” carbon steel and welded together. If the specification is for stainless steel, then we recommend a heavier gauge as it is more susceptible to deformation. Regardless, there is a risk of deformations of the materials due to the heat that is applied during the pouring process. When using stainless steel, it is likely to discolor during the pouring process. A common method to prevent deformation during the heating of the fabrication is to support it with temporary bracing or stiffening for the pour process. This will help to limit the movement of the steel.
- When pouring lead into the fabrication: Pour holes can be used, but the best method is highly recommended to leave one side completely open and then pour into the open face so that pour technicians can completely minimize lead shrink. It is best to orientate the container so that there are no areas that are hidden from the open pour face. Before the start of a lead pour, fabrications must be clean from debris, paint and other dirt.
Lead Pouring Process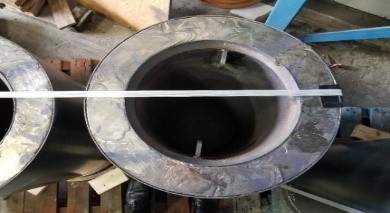
Once the fabrication is received and inspected to make sure that it is clean and suitable for pouring, it is preheated to start to pouring process which includes the following steps:
- Step 1: Before the pouring process begins the fabrication is heated up uniformly from the bottom by using gentle-flamed, gas burners focused on the inside and outside surfaces. Preheating prevents the lead from solidifying as soon as it makes contact with the sides and bottoms of fabrication. This allows for a more solid pour and decreases the risk of porosity in the lead. The next step is to slowly start to pour the lead into the fabrication. ASTM B-29 Lead (minimum 99.94% purity) is melted and poured slowly. Temperature is constantly monitored to ensure that the temperature does get too warm at any point.
- Step 2: As the lead levels rise, heat is discontinued from the bottom up to allow the lead to cool and solidify. Lead shrinks as it cools and will form a gap between the wall and the fabrication. By slowly cooling the lead from the bottom up, more lead can be poured into areas that are shrinking or not level as well as allow for air bubbles that could turn into voids to rise to the top. A highly controlled process can reduce the shrinking of the lead to around 1/32” to 1/16”. This is why it is important that the lead pourers have a clear view of all areas of the fabrication, as hidden areas are at a greater risk of lead shrinking away from the walls. This process is continued until the fabrication is filled to the desired filled to the top or desired fill level. The fabrication is then ready to be sealed and welded shut.
Considerations When Designing Fabrications for Lead Pouring
- Fabrications should be made of steel or stainless steel and must be strong enough to support the weight of the lead and at least ¼” thick to reduce the risk of temperature deformation.
- For health and safety reasons, MarShield does not accept fabrications that have been tinned or painted. The inside of the fabrications should be debris and moisture-free.
- Lead Shrinks as it cools. For radiation shielding, account for this in the design and allow for 1/16th to 1/8th inch of shrinking from all edges.
- There is the potential for deformation and the steel plates moving. This should be considered when deciding on tolerances and pieces that will need to fit together. MarShield can work with you to design bracing that will help with movements during the pouring process.
- Welds should solid on the fabrication before welding to ensure no lead will leak during the pouring process.
- Placement of lifting points should be considered and installed before the pouring of lead to ensure that the fabrication can be moved vertically.
While this type of lead pour procedure is used mostly in the Nuclear Industry, many of the above tips and procedures can also be applied to building test weights or any other lead-filled products to ensure the highest quality. MarShield is a leading expert in nuclear fills and works with numerous clients in the nuclear industry. If you would like to find out more information about MarShield’s Lead Pours, you can visit the MarShield website or you can contact MarShield directly, and we will help you find the best radiation shielding solution for you.